Polytetrafluoroethylene (PTFE) also called Fmur4, which is one of the most ideal corrosion-resistant materials in the world at this stage, commonly known as the “plastic king”. The materials are generally divided into two categories, namely suspended polytetrafluoroethylene and dispersed polytetrafluoroethylene .
Suspension polytetrafluoroethylene resin is generally white, the particle size is relatively large, and through specific treatment, all kinds of particle size powder can be obtained. The resin can play a very ideal effect in molding and can be well sintered into cylindrical billets, and then further processed into various specifications of seals.
Dispersed polytetrafluoroethylene can be divided into two categories, namely powder and concentrated dispersion. At present, the common PTFE raw material belt in the market is pushed and extruded with dispersed resin; in addition, the microporous film, fiber and pipe processed by dispersed resin are also used in various industries of the national economy as high-end materials. For example, its film can play the role of waterproof and breathable, and its micropore diameter can reach nanometer level, which is widely used in the field of filtration and separation; polytetrafluoroethylene fiber can be used in the production of packing, filter felt-based cloth, etc.; polytetrafluoroethylene pipes can be used in the field of corrosive liquid transport and heat exchange. Concentrated dispersion is mainly used in various coatings, the commonly used non-stick pot is made by coating and sintering with polytetrafluoroethylene dispersion, and Teflon impregnated glass fiber cloth used in electronic printing industry also uses polytetrafluoroethylene concentrated dispersion.
What are the structural characteristics of polytetrafluoroethylene (PTFE)?
Polytetrafluoroethylene is polymerized from tetrafluoroethylene and its corresponding molecular structure is shown in figure 1.
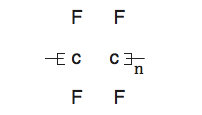
In addition, the chemical structure of polytetrafluoroethylene is to replace all hydrogen atoms in polyethylene with fluorine atoms. Fluorine is the most active and electronegative element of all elements, so the performance of the product changes obviously after fluorine substitutes for hydrogen. the main reason is the difference between Cmurl F bond and Cmure H bond.
Comparing CmurF bond with Cmurh H bond, because the electronegativity of carbon atom is obviously higher than that of the hydrogen atom, and the electronegativity of fluorine atom is higher than that of carbon atom, so the polarity of Cmure F bond is opposite to that of Cmure H bond, and the polarity of Cmure F bond is much larger. In other words, for the Cmurf bond, the F atom attracts more covalent electron pairs, while the covalent electron pair on the C-H bond is biased towards the carbon atom. The proton radius of fluorine atom is also significantly larger than that of the hydrogen atom, the length of Cmurf bond is obviously larger than that of Cmure H bond, and the bond energy of Cmure F bond is also significantly higher than that of Cmure H bond .
From an objective point of view, Cmurf bond is a kind of bond with excellent stability, the bond energy can be increased to 460 kJ/mol, and the attachment of the main carbon bond is surrounded by many fluorine atomic groups, so that the Cmure C bond is not affected by other molecules. In addition, the overall volume of fluorine atoms is relatively large and repel each other, the macromolecular chain is mainly helical, and the fluorine atoms existing in the main chain have good symmetry, so it is generally electrical neutralization.
2. What are the performance characteristics of polytetrafluoroethylene(PTFE) ?
2.1 Chemical properties of polytetrafluoroethylene are known organic compounds.
Learn the most inert polymer materials. Because of its special molecular structure, it can resist almost all strong acids, bases and organic solvents, even “aqua regia” can do nothing with it, and can maintain this property at high temperature, so this material is also called “plastic king”.
The exception is that molten alkali metals, such as molten sodium, can corrode the surface of polytetrafluoroethylene, causing fluorine around the carbon chain to react with it. The common method in industry is to use sodium naphthalene solution to modify the surface of polytetrafluoroethylene film or plate under the condition of nitrogen protection or oxygen isolation, so as to defluorinate or oxidize the polytetrafluoroethylene on the surface of the film or plate. so that it loses its non-stickiness and is easy to compound with other materials.
2.2 Thermal properties of PTFE
Polytetrafluoroethylene can perform well at high temperatures.
The operating temperature is usually-190 °C ~ 260 °C. The corresponding melting point temperature of the material is 327 °C and the corresponding thermal decomposition temperature is 420 °C, which is a very high service temperature in the existing engineering plastics. Polytetrafluoroethylene has almost no thermal decomposition under the condition of less than 420 °C, but can decompose greatly when it exceeds 420 °C, and the total mass loss per hour is about 0.01%. Its decomposition will produce fluorinated phosgene, perfluoroisobutene and other highly toxic substances, so in the hot processing of polytetrafluoroethylene, it is necessary to avoid the processing temperature higher than 400 °C to prevent the formation of certain risk factors. When polytetrafluoroethylene is continuously heated at 280 °C for 72 hours, its tensile strength is reduced by about 10% after it is restored to room temperature. In addition, when polytetrafluoroethylene is used for a long time at 260 °C and then transferred to room temperature, its tensile strength is kept at a given value. Therefore, in terms of thermal decomposition, the material can be used for a short time at 280 °C and continuously at 260 °C. In addition, in terms of thermal deformation, the material can be used for a long time at 260 °C under relatively low load; when the load is at a high level, the thermal deformation is very obvious, and its service time is greatly reduced.
2.3 radiation resistance
A large number of molecular degradation occurs in polytetrafluoroethylene (PTFE) under electron beam. Under the action of high energy radiation, Cmurc bond and Cmurf bond break at the same time, resulting in the decrease of molecular weight and PTFE performance. In addition, its radiation stability in vacuum is obviously better than that in air, because under the protection of inert gas in vacuum, radiation cross-linking reaction between PTFE molecules will occur in addition to the degradation reaction of PTFE. If the proper irradiation temperature and radiation dose are controlled, the treated PTFE material will be translucent, and the radiation resistance, high and low-temperature resistance, air permeability and liquid permeability of the material will be greatly improved.
3. Study on the modification of polytetrafluoroethylene.
The intermolecular attraction of polytetrafluoroethylene is very small, and it has a special helical molecular chain structure, which makes it have very low surface energy, so polytetrafluoroethylene also has very good hydrophobicity.
At present, there are two commonly used surface modification techniques: surface modification and filling modification.
3.1 Surface modification of polytetrafluoroethylene.
There are three kinds of surface modification methods of polytetrafluoroethylene. The first is the use of surface activation technology, which can be continuously defluorinated by radiation, and then fluorinated and grafted with other materials under specific conditions. It can also be treated by inert gas to break some of its main bonds and form a lot of free radicals, so as to improve its covered surface free energy and finally optimize its wettability. In addition, PTFE can be processed by corona to produce an activated layer that can be glued.
The second type is through chemical corrosion modification, this method can optimize its surface activity, and there are a variety of reagents to choose, including ammonia solution, pentacarbonyl iron solution and so on.
The third type is through surface deposition modification, specifically, PTFE is impregnated in a specific colloidal solution, so that colloidal particles can continue to deposit on its surface, and improve its wettability, and finally optimize its surface activity so that it will not encounter too many obstacles when compounding with other materials.
3.2 filling modification of polytetrafluoroethylene.
Generally, a variety of fillers are added to PTFE resin, including inorganic, polymer and so on, which can optimize its performance. In addition, compared with conventional products, the pressure resistance of the filled products increased by about 5 to 10 times, the wear resistance increased by about 1000 times, the corresponding linear expansion coefficient decreased by 80%, and the thermal conductivity increased by about 5 times. Therefore, it has a wide range of applications, including oil-free lubricated shafts, piston rings and so on. Such as PTFE bearing, it is filled with a variety of materials, mainly glass fiber, copper powder and so on, so that its various properties are significantly optimized. In addition, the guide belt is also a very typical kind of composite filling product, which is filled with glass fiber, MoS2 and other materials. At this stage, for the exploration of filling PTFE, relevant scholars are more inclined to launch new application fields and serialize all kinds of products designed.
4 main application fields of polytetrafluoroethylene.
In 2018, the total consumption of PTFE in China is about 70,000 tons. PTFE has excellent heat resistance, relatively wide operating temperature range, excellent electrical properties and constant temperature.
Gauge materials have incomparable chemical corrosion resistance, and flame retardancy is also very ideal, so it has been applied in many fields, including electronics, electrical, petrochemical, aerospace and other square areas.
The petrochemical industry is the most important consumption area of PTFE. Because of its excellent performance, it can be used to prepare equipment, pipe fittings and other devices. At the same time, the demand for PTFE in construction, light industry and other units has also increased significantly.
4.1 Data on the application of polytetrafluoroethylene(PTFE)
in anticorrosion show that the equipment scrapped in the United States due to corrosion is about 40% of steel production each year, resulting in a total loss of about US $75 billion. The economic loss caused by corrosion in our country has also been gradually raised to the current 15 billion yuan. Obviously, the loss caused by corrosion is a very prominent problem at present, so we must attach great importance to it.
As rubber, metal and other materials do not have good corrosion resistance and can not be used for a long time under harsh environmental conditions, the resulting loss is quite amazing. PTFE material has been widely used in petroleum, textile and other industries because of its excellent corrosion resistance. Among them, representative ones include exhaust pipes, steam pipes, high and low pressure pipes, valves and so on. Especially in the harsh environmental conditions, such as low temperature and anti-sticking, which can not be used by conventional materials, it shows the advantages of PTFE.
Another important application of PTFE is to act as a sealing material. Although the seal is the accessory of all kinds of equipment and is of low importance compared with the equipment, the sealing effect has a very prominent impact on the overall effect of the use of the equipment. Representative include heat exchangers, large-diameter containers, glass reaction pot seals and so on. In addition, the composite of PTFE film with it can significantly optimize its solvent resistance and improve its dielectric resistance to a certain extent, and the valence grid is relatively moderate, so it is very suitable for many occasions with stringent sealing requirements. At the same time, the material also has outstanding high and low-temperature resistance, which is the core substitute of asbestos gasket at the present stage. In addition, if it is reinforced by carbon fiber, its strength can be improved to a higher level, and the fatigue resistance is also very good, and the coefficient of thermal expansion meets the use standard. This kind of performance is incomparable to other materials.
4.2 Application of low friction performance of polytetrafluoroethylene in load
Due to the fact that lubricating oil cannot be added in some parts of the equipment, lubricating grease will be completely dissolved by solvents, so products in many fields such as pharmaceuticals and textiles must pay attention to this. Because the friction coefficient is relatively low compared with most solid materials, filled PTFE has gradually evolved into an excellent material without oil lubrication for all kinds of parts. It has a wide range of applications, including bearings of chemical equipment, piston rings, supporting sliders of steel roof trusses, bridge rotation and so on.
4.3 Application of polytetrafluoroethylene in electronics and electricity.
The dielectric constant of polytetrafluoroethylene is relatively small, so it can be used in the preparation of enamelled wire for use in micro motors. In addition, the fluoroplastic film has a certain selective permeability to all kinds of gases, so this characteristic can be used to prepare oxygen sensors. In addition, combined with the characteristics of poloidal charge deviation of fluoroplastics under specific conditions, it can be used to prepare loudspeakers, equipment parts and so on.
Because the refractive index of polytetrafluoroethylene is relatively low, it can be used to prepare optical fiber. PTFE is a kind of insulating material with a wide range of applications, and its core application is the outer layer of wires and cables, so it can play a good role in broadcast electronic devices, and can also play an ideal role in connecting lines. Under the condition of high frequency electric field, its dielectric loss reaches a low level; in the printed circuit board, it has outstanding dielectric properties and is difficult to be affected by other chemicals. At the same time, insulating film is also the main application form of electrical insulation of polytetrafluoroethylene, which is widely used in the insulation media of all kinds of capacitors. In addition, PTFE film has good applicability for insulated cables, motors and transformers, and is also a key material for many important electronic components.
4.4 the application of polytetrafluoroethylene in medicine
continues to develop with the continuous development of contemporary medical technology, and the dependence on polymer products is further increased. Such products come into contact with normal human tissues, so their non-toxic and environmentally friendly properties are very important.
In recent years, polymers have greatly reduced the application space of conventional materials in medical treatment. Because PTFE can reflect a certain biological inertia, the pore-forming ability after standardized treatment is very good, so on this basis, we can prepare a device that does not lead to organism rejection, and develop a device that is in deep contact with blood, which will not have a negative impact on blood. The expanded PTFE material is pure inert in nature, which is of great benefit to its biological adaptability, does not lead to machine body rejection, and can be sterilized by diversified methods, and it covers multi-porous structure, does not have hydrophilicity, blood generally does not block, and can play an antithrombotic effect, this kind of blood vessels can enable cells to enter smoothly. At the same time, the intima is formed with the attached tissue, so the sterilization operation is relatively simple, and it provides some convenience for wound suture, there is no cracking, and there is no shrunken collapse when it is used for a long time.
Dilated PTFE is also a very important part of gastroscope forceps catheter, because its deformation characteristic is very ideal, there is no foreign body reaction when used in human body, and many operations such as stomach sampling and polypectomy are carried out, which greatly reduces the difficulty of operation and reduces the pain of patients in the course of operation. In addition, the material can prepare cardiac repair membrane, repair the diaphragm defect well, and standardize the plastic treatment of arterial stenosis. In addition, it can support a variety of Kangfu solutions, which involve artificial blood vessels, blood vessels, surgery and other aspects.
4.5 Application of Anti-adhesion property of Polytetrafluoroethylene.
PTFE has low surface tension and is not attached to anything else.
Quality, can show the characteristics of high and low temperature resistance, in the non-stick pot anti-stick has a very ideal applicability. In addition, the anti-adhesive process usually covers two types: the first is to assemble the PTFE parts on the substrate; the second is to cover the PTFE coating on the substrate according to the relevant specifications by heat shrinkage treatment.
With the rapid development of modern science and technology, PTFE materials also show three shortcomings that can not be ignored: cold flow, difficult weldability and difficult melting. These problems are being solved step by step, which makes it have good application potential in optics, medical treatment and other fields.
Application of polytetrafluoroethylene in high temperature dedusting in China, the dust removal index set in the early stage is relatively low, and the dust removal concentration is about 400 mg/Nm3, which does not meet the requirements of dust discharge concentration not more than 50 mg/Nm3 and reducing PM2.5 (diameter not more than 2.5 μ m). Thus, it has formed a good development contract for the dust pollution control industry. The development of filter media with longer service life and better purification efficiency has gradually become the main development trend. On the other hand, most industries put forward more stringent requirements for the main components of dust removal devices, especially in the fields of industrial waste incineration and power generation, whose relatively harsh environment puts forward new requirements for materials.
At the same time, with the continuous progress of industries around the world, atmospheric pollution has gradually evolved into a global problem that can not be ignored, and the clean-up of pollutants continues to transition to the direction of waste gas. In the process of the treatment of fine dust, there are many methods to choose from, of which the more important ones include two types, namely, electrostatic precipitator and filter bag dedusting, but there are few methods for the treatment of waste gas. At present, the research of waste gas catalyst decomposition technology at home and abroad has made a breakthrough, but the current catalyst carrier is not ideal. The carrier prepared by PTFE fiber is expected to solve this problem.